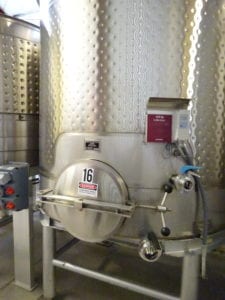
We’re currently working with a speciality harvesting equipment appraisal in the Salinas area and have been working with the client to compile an asset list for the upcoming equipment inspection. Several conversations and email exchanges regarding how to compile an effective equipment list – in conjunction with some recent interesting inspection experiences – have freshly reminded me of how important a good asset list is to an efficient equipment appraisal, and certainly to asset inspection.
We’ve shared information about what constitutes an adequate asset list before and it’s worth repeating that an appraisal lives or dies by the asset list. Let me share just a few experiences we’ve had lately regarding the correlation of asset lists and inspection efficiency and some suggestions for you to consider.
Location of Equipment
One important aspect of an inspection that’s often overlooked is location of the equipment. For example, we recently inspected a 5 location cabinetry manufacturing business spread out along the central California coast. On the asset list provided, each location has its own list of equipment. Even better, those pieces of equipment were listed in the order in which we encountered them as we walked through the shop. In addition to setting up the asset list geographically, the business owner provided detailed and thorough information on all the equipment. He remarked that when he wasn’t sure of a manufacture date, or purchase date, he was able to reconstruct the information from his accounting records. The inspection was completed entirely in one day, much quicker than expected!
Just a few weeks earlier, on the other hand, we’d attempted to inspect a food processing plant for a retroactive property tax appeal. The folks who provided that asset list had not taken the time to locate the machinery on the floor before we arrived and so we spent several fruitless hours wandering through the many different processing rooms with the plant manager and controller, trying to correlate the list with the equipment on-site. Many of the processing lines had been moved & reassembled from their original configuration, some of the equipment on the list had been placed into storage or discarded, and too many of the descriptions were vague or imprecise. Often we weren’t sure which pie filler or mixer on-site correlated to the line items on the asset list.
Verification of Equipment
You may have noticed that an important part of the inspection is the identification and verification of the assets. Location helps with verification but there are other ways to make verification easier as well. For instance, we often appraise farm equipment, trucking fleets, or construction equipment – mobile equipment. In such cases, it’s impossible to align harvesters or concrete pumpers and cranes exactly with the asset list. The important thing is that the items on the list be easily verified with each physical piece. So if, for example, you have ID numbers on your equipment as many operations do, feel free to make a column on the asset list to note those numbers.
At a recent vineyard inspection for estate tax purposes, we saw 6 very similar Korvan grape harvesters, ranging from the 1999 model to 2013. The harvester chassis were numbered but there was not a corresponding number on the asset list so it took some time to determine which were which. Alternatively, during a large construction company inspection several years ago, every single large asset was numbered and the list provided included those numbers, making the match-up much quicker and efficient.
Another factor is that the descriptions make sense. You’d think this would be a given, but at one inspection for winery equipment appraisal, the descriptions for some of the wine tanks were in gallon, as expected, while others were by wine tank dimensions. The problem is that wine tank labels display gallons and winery staff are generally more familiar with wine tank capacities than dimensions. This kind of disconnect makes the equipment inspection process much longer and much more expensive. It turns out that the dimension descriptions had been transferred over from the General Ledger, which leads to the more general discussion of why general ledgers aren’t the best source for asset lists.
General Ledgers & Asset Lists
When the asset list is extracted from a company’s general ledger, all bets are off. We discuss this situation in more detail here, specifically in regard to depreciation schedules. One problem with using a general ledger or depreciation schedule for an asset list is that the items on the list are often difficult to tie out to the equipment on-site. For example, at the aforementioned winery inspection, we had more entries than we’d like that read something like, “crush equipment … $795,000” instead of lining out the separate pieces of equipment with their own costs. This is problematic on more than one level.
While an inexact general ledger creates problems in the appraisal process – especially for property tax appraisals – it also unnecessarily impedes a company’s ability to keep their ledger tidy for ad velorem property tax filing. We see this most often in conjunction with discarded equipment. How can your controller track which pieces of equipment are no longer in use when those pieces of equipment were never discretely listed on the ledger?
That last tip is obviously from my CPA training and you’re welcome!
Jack Young, ASA, CPA
NorCalValuation.com